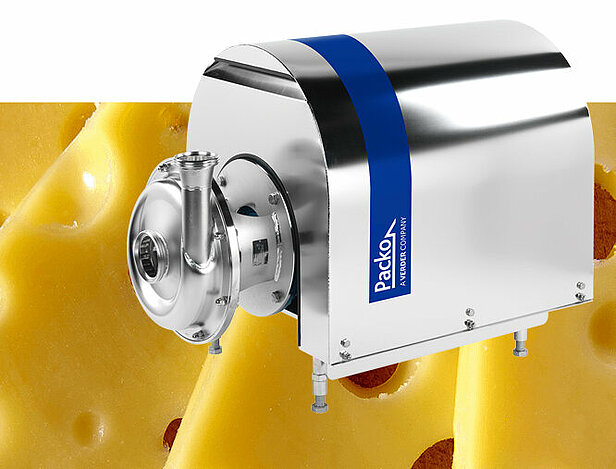
Anche la vostra pompa vi sta rovinando?
Nota: questo caso di studio è applicabile solo ai formaggi duri.
Esistono alcuni pregiudizi ostinati su quale sia la pompa giusta in un processo di produzione di formaggi duri. Se questi pregiudizi non sono corretti, i produttori di formaggio non otterranno il massimo dal loro processo. Questo vale sia per l'efficienza del processo che per la qualità del prodotto.
Per questo motivo, in collaborazione con un produttore di formaggio Emmental, abbiamo cercato di capire se questi pregiudizi contengono qualcosa di vero.
Allo stesso tempo, abbiamo anche cercato di risolvere un problema comune nel processo di produzione dei formaggi duri. La produzione di formaggi duri spesso dà luogo a un prodotto secondario indesiderato, ovvero la cagliata fine.
Questo prodotto collaterale è preferibilmente da evitare, poiché ha un effetto negativo sulla qualità del formaggio e, di conseguenza, sul rendimento del produttore. Il punto è che più si produce questo prodotto secondario (cagliata fine), meno rimane del prodotto principale (il formaggio).
Uno dei motivi principali per la formazione di ammendamenti è il pompaggio troppo brusco del prodotto. Non c'è da stupirsi, quindi, che la scelta della pompa svolga un ruolo importante nella prevenzione della formazione di cagliate.
Con un esempio pratico concreto, vorremmo dimostrare come una scelta corretta della pompa risolva questo problema e allo stesso tempo aumenti la qualità e l'efficienza del processo.
Visione attuale del mercato
Attualmente esistono circa 4 tipi diversi di pompe nel processo di produzione dei formaggi duri:
- Pompa monotipo
- Pompa a seni
- Pompa a lobi
- Pompa a vortice (pompa centrifuga con girante a vortice)
In genere si ritiene che le pompe a vortice e le pompe a lobi siano le pompe migliori per evitare la formazione di ammassi di cagliata. Diamo un'occhiata più da vicino a questi due tipi di pompe.
In primo luogo, le pompe a lobi. Hanno il vantaggio di funzionare lentamente e di fare pochi danni, ma lo svantaggio di essere piuttosto costose (soprattutto per grandi portate superiori a 50 m³/h). Inoltre, necessitano di una pompa CIP separata (CIP = cleaning in place).
In secondo luogo, le pompe vortex, un tipo di pompa centrifuga con girante incassata (girante vortex) a pale diritte e un corpo pompa completamente rotondo (Figura 1).
Si presume che la girante incassata garantisca che la cagliata non passi "attraverso" la girante e che quindi sia meno dannosa di una girante normale.
Ma queste ipotesi sono corrette o si tratta di pregiudizi?
Possibili alternative?
Una pompa vortex è davvero la soluzione migliore per questo problema? Nell'affrontare questa domanda abbiamo tenuto presente quanto segue:
"Una pompa con la massima efficienza possibile garantirà un pompaggio più fluido del prodotto e quindi meno danni alla cagliata".
Per trovare un'alternativa, abbiamo utilizzato il nostro sistema CFD (= Computational Fluid Dynamics). Questo software consente di simulare il fluido nella pompa. Questo ci ha dato l'opportunità di migliorare i seguenti punti:
- Ridurre la turbolenza;
- aumentare l'efficienza
- Ciò che si tradurrà in un pompaggio generalmente più morbido del fluido.
Questo studio ci ha portato a realizzare una pompa Packo con le seguenti caratteristiche:
- Pompa ad alta efficienza;
- Corpo pompa a forma di voluta;
- girante chiusa con pale 3D.
In una fase successiva abbiamo confrontato la nostra soluzione con la pompa a vortice abituale e con lo stesso punto di funzionamento: 60 m³/h a 7m. Il risultato è stato il seguente:
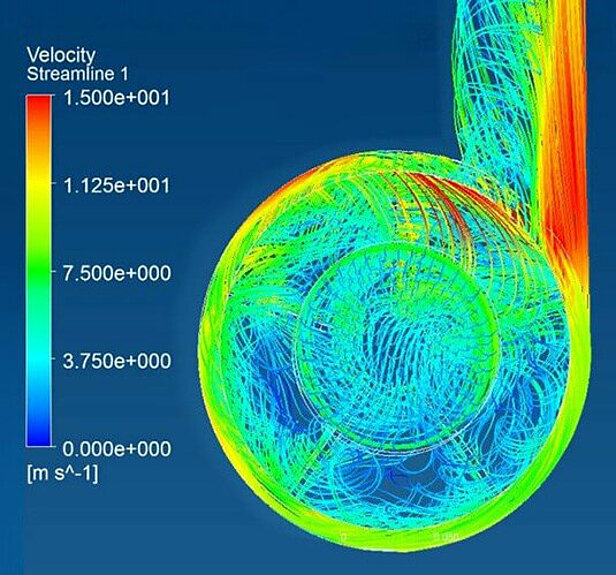
Girante a vortice
- Velocità > 15 m/s
- Zone morte
- Grande variazione di velocità
- Efficienza: 58%
⇒ Pompaggio brusco
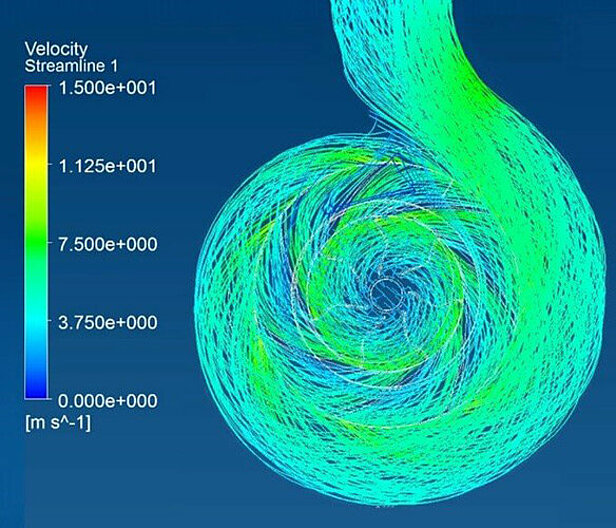
Girante chiusa
- Velocità < 7 m/s
- Nessuna zona morta
- Piccola variazione di velocità nella pompa
- Efficienza: 75%
⇒ Pompaggio dolce
Ciò che è apparso subito chiaro da questo test è che una girante chiusa raggiunge un'efficienza maggiore rispetto alla girante a vortice spesso utilizzata.
Nella gamma standard di Packo offriamo due pompe che soddisfano queste caratteristiche, la FP3 e la MFP3. Queste pompe potevano quindi essere utilizzate per il nostro test presso il cliente.
In pratica
Per questa ricerca abbiamo lavorato a stretto contatto con un cliente che produce formaggio Emmental. Come la maggior parte dei produttori di formaggio, anche lui utilizzava pompe vortex nel suo processo produttivo.
Prima di effettuare il test con Packo, il cliente aveva già fatto diverse prove:
- Impostazione di una velocità più bassa e più alta della pompa;
- Impostazione di tempi di riempimento più lunghi e più brevi;
- Pressione diversa all'ugello di riempimento (0,25 - 0,5 bar);
- Ugello di riempimento con diametri diversi (17-22 mm).
Tutte queste regolazioni non hanno mostrato miglioramenti evidenti, come ci si aspettava, anzi in alcuni casi è stata osservata una riduzione della qualità. Una minore qualità del formaggio si nota anche dalle seguenti caratteristiche:
- Presenza di fini di cagliata in vari punti della superficie, che causano problemi durante la pressatura del formaggio giovane con la separazione della fase solida (cagliata) da quella liquida (siero);
- Riempimento non uniforme della forma;
- forme di formaggio più sottili al centro che all'esterno;
- forme di formaggio con peso diverso
- Crepe nel formaggio.
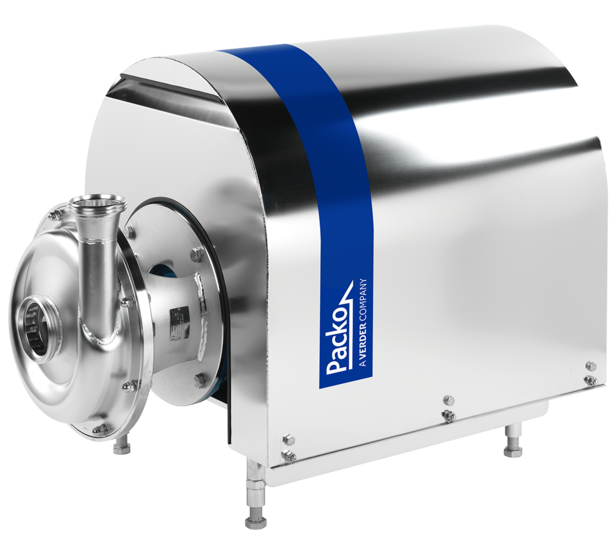
Obiettivi della ricerca
Per poter parlare di un esercizio di successo, il nostro cliente aveva fissato i seguenti obiettivi:
- Tempo di riempimento della forma di formaggio di circa 12-13 minuti;
- La pressione sull'ugello di riempimento (dosatore) è sempre compresa tra 0,30-0,35 bar;
- Distribuzione uniforme della cagliata nelle diverse forme (6, 8 e 10);
- Assenza di ammassi di cagliata;
- Lo stesso peso per tutte le forme di formaggio (circa +/-3 kg);
- Riempimento coerente (simmetrico);
- La qualità del formaggio corrisponde ai requisiti del mercato (numero di fori, durata e conservabilità).
Test pratico dei parametri del sistema
Nel frattempo, è stata effettuata una valutazione dell'intero impianto presso la sede del cliente. Per determinare quale pompa e in quali circostanze avrebbe ottenuto il risultato migliore. Per poter così effettuare una scelta ottimale.
- Punto di funzionamento desiderato: 60m³/h @8,6m.
- Selezione della pompa una pompa Packo FP3/100-250 con le seguenti caratteristiche:
- Motore da 5,5kW - 6 poligoni (1000 rpm => 700 rpm);
- Girante chiusa;
- Efficienza della pompa di circa il 75% al punto di funzionamento.
Questa pompa è stata utilizzata nel processo di produzione del caseificio e sottoposta a vari test per studiare le impostazioni ottimali. Ciò è necessario in quanto vengono utilizzati diversi tipi di formaggio (6/8/10) che richiedono velocità e punti di funzionamento diversi.
Di seguito troverete una panoramica delle impostazioni testate e dei risultati finali.
Fase di prova | Impostazione finale | |
Pressione al dosatore |
0.1 – 0.6 bar |
0.30 – 0.35 bar |
Tempo di riempimento |
9-13 minuti |
12 minuti |
Velocità della pompa | Velocità diverse | 600 a 700 RPM |
La pompa ha funzionato bene?
Ora rimane la cosa più importante. Il test ha dato risultati positivi presso il cliente?
Dopo aver inserito la pompa FP3 nel processo di produzione, abbiamo riscontrato i seguenti risultati:
- Niente più perdite a causa delle ammaccature della cagliata;
- Formaggi simmetrici;
- Lo stesso peso di formaggio nella produzione delle varie forme (6, 8 e 10);
- La qualità del formaggio corrisponde ai requisiti del mercato (numero di fori, durata e conservabilità);
- Livello di rumore molto basso durante il pompaggio della cagliata.
- Ancora meglio, tutti questi cambiamenti hanno fatto sì che dopo 3 (!) mesi la pompa si sia ripagata da sola.
Una buona scelta della pompa ha quindi avuto un impatto positivo sull'intero processo produttivo: dall'efficienza del processo alla qualità dei formaggi stessi.
Contattateci e lo dimostreremo anche per il vostro processo.