Upstream - From raw materials to processed lithium compound
The upstream portion in the extraction and purification of battery grade Lithium plays a critical role in the overall quality and sustainability of EV batteries. It involves the initial stages of lithium battery production, including the extraction lithium from spodumene ore and their processing into lithium hydroxide suitable for EV battery manufacturing. The process map below explores the various aspects of the upstream process and which pumps are involved in the different steps of the process.
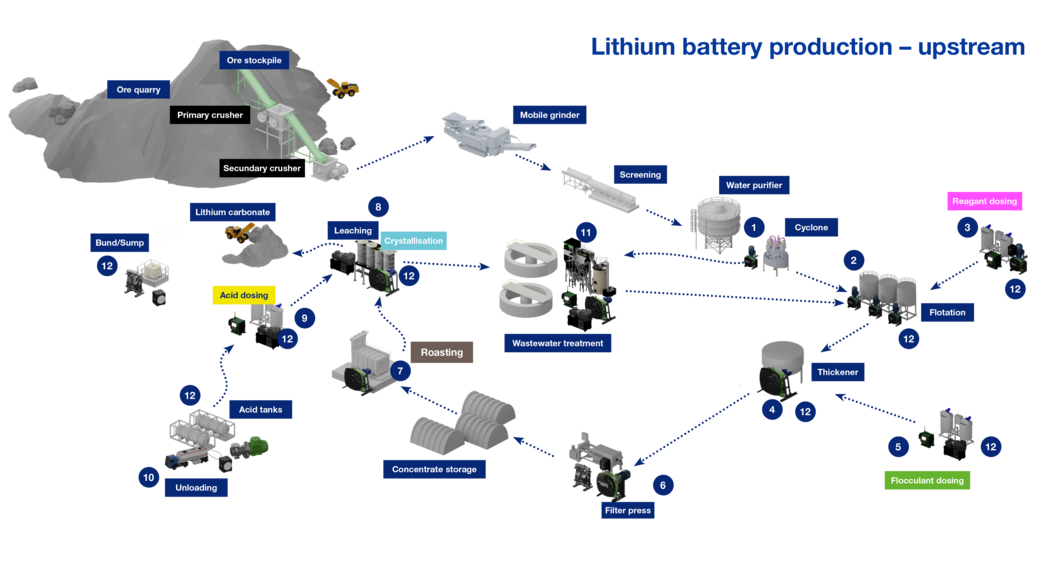
Applications
1. Water treatment - flocculant & lime dosing and pH correction
The protection of water is crucial for environmental conservation, and process facilities recycle and re-use water to achieve this. pH correction is essential in the manufacturing of Lithium Hydroxide due to its highly acidic nature. Lime dosing is the first step in the water recycle process, as it reduces corrosion and enhances flocculation efficiency. Peristaltic pumps are superior to helical screw pumps in protecting the polymer during the pump process and can result in cost savings of up to 50% for flocculant. The gentle pump action of peristaltic pumps improves flocculation efficiency and protects the pump against abrasive damage
2. Flotation - reagent dosing
The floatation process involves inducing air to create a froth and separating particles from liquid using different reagents and acids. The Dura peristaltic pump is useful for maintaining accuracy in dosing and achieving floatation. Its reinforced peristaltic hose is accurate at high speeds and temperature and is superior to membrane dosing pumps in chemical capability. Verderflex tube pump technology is used for dosing lower volumes and maintaining accuracy between 2-3% during tube life. Peristaltic pumps are preferred for their positive displacement, near-perfect volumetric efficiency, and capability to transfer abrasive and corrosive liquids commonly used in reagent and acid dosing.
3. Reagent make-up dosing station
The Dura peristaltic pump has high volumetric efficiency, which helps maintain dosing accuracy in the floatation process. Its reinforced hose remains accurate at high pump speeds and temperatures and is superior in chemical capability compared to membrane dosing pumps. Verderflex tube pump technology is used for dosing smaller volumes with accuracy between 2- 3% during tube life. Peristaltic pumps have positive displacement, near-perfect volumetric efficiency, and can transfer abrasive and corrosive liquids, making them the preferred pump technology over membrane or solenoid dosing pumps, especially for reagent and acid dosing.
4. Underflow thickener
The concentrate underflow thickener thickens slurry to form a concentrate that can be transferred to a filter press for de-watering. Higher solids content in the slurry results in less water needed for de-watering and recycling. Peristaltic pumps are preferred over centrifugal pumps as they can transfer slurries at high solids density and retain solids in suspension at low deposition velocity. Centrifugal pumps in the application cannot use mechanical seals and require costly and frequent repairs. Peristaltic pumps are a better option due to their lower operational costs, extreme asset and maintenance cost of piston diaphragm pumps, and ability to maintain system pressure calculations.
5. Flocculant make-up dosing station
Peristaltic pumps have a gentle pump action that improves flocculation efficiency and protects the polymer during the pump process, resulting in as little as 1% damage/loss. Flocculant manufacturers recommend using a positive displacement pump, and customer testimonials report up to 50% cost savings when using a peristaltic pump. Over flocculation can create lumps ("fisheyes") in the slurry, which can harm the pump, but a peristaltic pump is superior in accuracy to maintain the correct flocculation dosage and transfer thick solids in the event of over flocculation.
6. Filter press
Verderflex peristaltic pumps improve filter press cycle time by transferring high-concentrate slurries from the thickener. Their linear performance is superior to traditional centrifugal or helical screw pumps. Gradually reducing the pump speed/flow as the filter press builds up pressure improves cycle time and allows for increased production. Verderair diaphragm pumps are designed for constant, non-stalling operation and self-regulate as pressure builds in the chamber. As pressure is released in the tank, the pump self-primes and returns to its original flow rate.
7. Roasting - transfer of concentrate
Roasting is usually a combination of conveying and not often pumped due to the extreme high temperatures that do not always make it possible to pump. In the event of a pump process, peristaltic pumps are capable of maintaining the transfer of slurry with the same properties as experienced during the thickening and filter press process. However, caution should be taken with acid concentrate and temperature considerations in line with hose abilities in this process.
8. Acid leaching & crystallisation - dosing & transfer
Slurry treatment with high-concentrate, high-temperature H2SO4 limits pump options in the process, and the use of peristaltic pumps depends on the properties of H2SO4. The Verder e-PURE PTFE pump is the most popular choice of pump due to its chemical compatibility, solids capability, and use of electricity instead of compressed air. The cost of ownership of the Verderair e-PURE pump is lower than the maintenance cost of expensive compressor and pneumatic supply systems.
9. Acid make-up dosing station
H2S04 dosing Slurry treatment with high-concentrate, high-temperature H2SO4 limits pump options in the process. Depending on the properties of H2SO4, the use of peristaltic pumps may be limited. The Verderair e-PURE PTFE pump is the most popular choice of pump due to its chemical compatibility, solids capability, and use of electricity instead of compressed air.
10. Acid offloading & transfer to dosing stations
Acid transfer/offloading involves high volumes and is typically done using an diaphragm pump or mag drive pump. Acids need to be handled carefully as they can harm the environment and employees in case of leaks from systems or pumps. Diaphragm pumps and mag drive pumps are advantageous as they do not use seals and have the option to install leak detection systems, making them safer to use.
11. Waste water treatment - purification and recycle
The protection of water is crucial for environmental conservation, and process facilities recycle and re-use water to achieve this. pH correction is essential in the manufacturing of Lithium Hydroxide due to its highly acidic nature. Lime dosing is the first step in the water recycle process, as it reduces corrosion and enhances flocculation efficiency. Peristaltic pumps are superior to helical screw pumps in protecting the polymer during the pump process and can result in cost savings of up to 50% for flocculant. The gentle pump action of peristaltic pumps improves flocculation efficiency and protects the pump against abrasive damage
12. Bund sump spillage – dewatering
Diaphragm pumps are the most popular and cost-effective technology for clearing out sumps that have accumulated water due to spillage, maintenance, or rainwater. The technology's ability to pump negative NPSH, low CAPEX, and OPEX costs make it a preferred pump over expensive rubber-lined counter lever vertical spindle pumps.